外観検査の自動化はどのように行うのか?自動化の種類を紹介
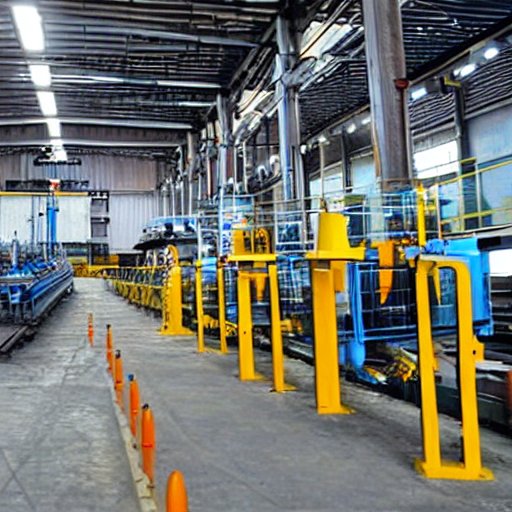
外観検査を自動化するには?
外観検査を自動化するには、良品・不良品を判定する検査の部分だけではなくその前後の工程が自動化している(人間の手を介さない)システムとなっていることも非常に重要です。仮に検査の部分だけを撮像機器と画像処理ソフトウェアで自動化できたとしても、その前後に人の手がかかっていれば完全に自動化しているとは言えません。
受入検査などで多い、製品が整列された搬送設備を持っておらず1つ1つを手に取って目視検査で確認するケースや検査基準が非常に入り組んでおりベテランの検査員のカンコツに頼った目視検査を行うケースなど、外観検査を自動化するのが難しい工程が多くあることも現状です。
外観検査の自動化に取り組むうえで、検査の部分を含めた以下の3点において人間が介さないシステムを構築する必要があります。
- 検査ポイントまで製品を動かす搬送工程
- 良品・不良品を判定する検査工程
- 良品・不良品に応じて搬送パターンを変える排出工程
3については、不良品の排出や、別ラインへの搬送などを行いますが、製品によっては不良発生のモニターや警告灯への表示などだけでよいケースもあり、必ずしも必須ではありませんが、1と2については検査の自動化を果たす上でまず必須となる要素です。
以下では、検査を自動化していく上で工夫すべき点や注意点について紹介します。
搬送工程
製品の位置バラツキや検査面の見え方など、搬送状態がそのまま検査の精度を左右するといっても過言ではないほど、いかに上手く製品を搬送するかは安定した検査を行うためには重要です。
一般的には、コンベアラインなどで整列されて流れてくる対象物をカメラで決まったタイミングで撮像することで、すべての製品を安定して撮像することができます。いくらAI検査を使用したからといって、見えていないものを検出することは不可能ですので、製品の全周を検査する必要があることも少なくなく、製品の向きを変えて全周をカメラで撮影したり、複数のカメラで撮像することが必要になります。製品の向きを変えるためには、コンベアラインで製品の向きを変更する(例えば裏面)ためのカラクリを作るケースや、ロボットアームで1台のカメラを動かし複数の画角を撮像したり、インデックステーブルで全周撮像するケースなど様々な手法があります。これらは、検査したい箇所を検査できるかということは当然ですが、既存の生産ラインとの接続性の良さ、タクトタイム、コストを勘案して最適な手法を選択する必要があります。
一方で、既存の検査工程の改善という切り口で考えると、検査精度の高度化や検査員の人数を1人でも減らすなど省人化といった単語が出てきます。搬送ラインのない環境での卓上検査の導入であったり、例えば表面と裏面を検査する必要がある製品について表面を画像検査が、裏面を目視検査でカバーするという「協業」によって検査を行う、など完全な自動化とまでは言わずとも限られた投資で最大限の自動化を行うという方法もあります。
ここでは一例として、卓上検査機の事例を取り上げます。卓上検査機は搬送環境がなく、検査項目が非常に多く繊細な不良を目視によって検査されている環境においては、最小限の投入コストで検査の省人化、高精度化を実現できるため非常に有効な手法となります。例えば電子基板のように、チップや配線など非常に小さい部品を短い検査タクトで詳細に見る必要があるものを対象に、オフライン検査で画一された基準で検査を効率的に行える半自動での検査を行っている例が多く見られます。
このように自動化の程度によって、搬送のあり方は大きく変わってきます。1から生産ライン・検査ラインを複合で立ち上げる場合を除いて、既存の生産ラインに対して、後からアドオンの形で検査のシステムを最適な方法で導入することを検討しているケースが多くあります。
検査工程
検査の自動化と聞くと、こちらをイメージされる方も多いのではないでしょうか。検査対象を認識しカメラで撮影することで画像にします。その画像をもとに画像処理やAIを用い、人間の目で判定するのと同様に、良品・不良品の判定を行います。
画像処理やAIなどのソフトウェアは高速かつ安定した検査ができることが大きなメリットです。製品を構成する部品や素材の色味や取付位置など、様々な特徴を持つ製品を瞬時に正確に判定することができます。
一方で、判定を行う上で良品・不良品の判定精度が安定しないものでは目視検査を並行して行う必要があるため、当然ですが精度の高いソフトウェアが必要になってきます。昨今の要求品質の高まりや色味や大きさ、絵柄等の多品種など、年々検査が難しくなってきており、その結果検査基準が入り組んだ複雑なものになりつつある傾向があります。こういった目視検査用に作成した検査基準では、AIや画像処理を同じように適用しようとすると全ての要求を100%満たすことは難しいケースがどうしても多くなります。
また、多くの場合検査員の官能に頼った曖昧な検査基準になっていることも多く、検査員に依って不良の判定基準が異なるケースも多くあります。このように検査員によって判断の違いが生じるような検査基準ではソフトウェアで基準通りに判定することは非常に困難です。このような場合は、可能な範囲で画一的な検査基準に変更することや、検査員の目視検査と組み合わせるといった対策が考えられるでしょう。
検査の自動化を検討している担当者の方と現場の検査員の方で検査基準の認識のズレを解消し、曖昧な基準を合理的な基準に落とし込み、時には人と検査を併用して、最大限の検査の自動化メリットを出していくことが自動検査導入における重要なポイントとなります。
排出工程
人間が不良品と判定した際には、手動もしくは機械を介して不良品を良品の搬送ルートとは異なるルートへ排出し、手直しや場合によっては廃棄するなどします。AIや画像処理でも同様のことが言えます。生産タクトが遅いものについてはそのまま不良品を人の手で排出することができますが、多くの場合は排出は別の工程であったり、不良の数をカウントし品質として反映させるなどの手法があります。
排出の自動化には、別の工程で行うよりも、判定と同時に行う方が効率が良いため、画像検査を適用する場合はAIや画像処理の判定結果からPLC信号を使って良品・不良品に応じた外部機器との連携を行うことが一般的です。
まとめ
このように外観検査の自動化を考える上でも搬送、判定、排出と3つの工程がそれぞれ密接に関わりあっており、どう自動化を実現するかを考える必要があります。完全に自動化を行うのか、人間と協調するのか、それとも人間の目視で検査を行うのかなど自動化のレベルをどこに設定するかによって搬送や排出の部分の設計が異なり、それによって必要なコストも大きく変わってきます。
特に搬送も含めた自動化を行う際には、搬送や排出といった装置の部分や判定のソフトウェアの部分、検査に必要な照明やカメラ等の画像を取得するために必要な部分と多岐に及ぶ分野を横断的に考慮する必要があります。多くの場合それぞれを得意とするメーカーが分担しながらプロジェクトを推進するため、時間や金額のコストが大きくなる傾向があります。
必要な自動化のレベルとそこにかかる時間や金額のコストを照らし合わせて、費用対効果を考えながら外観検査装置の設計を行うことがプロジェクト成功のカギと言えるでしょう。