外観検査の検査基準とは?基準書の項目と外観検査手順書作り方
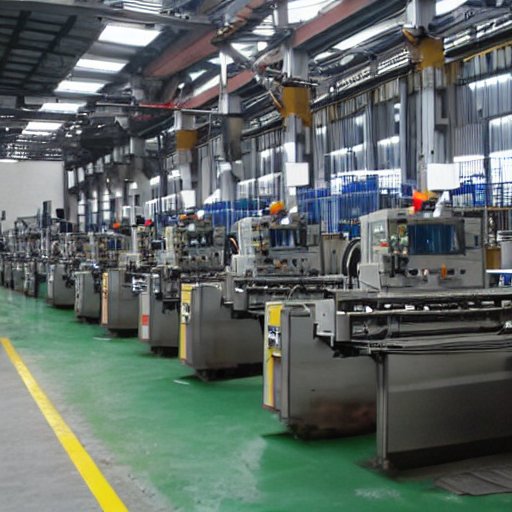
外観検査とは
外観検査は、製品や部品の外観や外観的な特徴を評価する品質管理の手法です。製造業において、製品の外観や仕上がりの品質を確保するために行い、製品が所定の基準や要件を満たしているかどうかを判断します。具体的な要素としては、製品の形状、色、テクスチャ、表面の傷や欠陥、ラベルやマーキングの正確さなどがあります。これらの要素は製品の外観品質やブランド価値に直結する、顧客満足度や市場競争力に影響を与える重要な要素となるため、不良品の市場への流出は重大な問題となります。
検査基準書の例
外観検査は基本的に全てを1人で行うことはなく複数人で実施するため、作業者によって不良品の判定基準が変わってしまうと不良品が市場流出するリスクが高まってしまいます。そのため検査基準は、誰が検査を行っても同一の品質が担保されるように、製品の外観品質や要件を明確化し、検査者が一貫して評価できるようにするために使用されます。例えば、検査の基準を文章や限度見本を使った視覚的な基準を設けるなどがあります。一般には以下の例がありますが、製品や業界によって異なる基準が存在します。
- 外観仕様書: 外観検査においては、まず外観仕様書が作成されます。外観仕様書には、製品の外観に関する詳細な情報が記載されており、形状、寸法、色、表面の仕上げなどが明示されます。これにより、検査者は製品の外観に関する基準を把握し、判断することができます。
- 視覚基準: 製品の外観を評価するためには、視覚基準が重要な役割を果たします。視覚基準は、製品の外観に関する具体的なガイドラインや規定を提供します。例えば、傷の深さや長さ、色の範囲、表面の凹凸の許容範囲などが示されます。視覚基準は、不良品の判別や評価の一貫性を確保するために使用されます。
- 標準規格: 様々な産業や製品には、外観品質に関する標準規格が存在します。これらの規格は、製品の外観に関する要件やテスト方法を定義し、一般的な基準を提供します。例えば、ISO 9000シリーズの規格や業界団体の規格などがあります。
- 検査手順: 外観検査では、明確な検査手順が策定されます。検査手順には、どのような順序で製品を検査するか、どの視点で評価するか、どの検査方法や機器を使用するかなどが記載されます。検査手順は一貫性と効率性を確保するために重要です。
画像検査における注意点
カメラで画像を撮影し画像処理やAIを用いて、不良品であるかどうか判定を行う画像検査でも同様に検査基準が必要です。画像処理ではプログラム、AIでは学習画像として検査基準を表現し、出力結果に対して、不良の大きさや長さ、色味などのしきい値を使用し最終的に良品・不良品の判断を行います。
一般に検査基準は目視検査で人間が行うという前提で作成されたものですので、人間であれば手で触ったり、角度を変えながら見ることで判断ができるような、色味・キズの大きさ、深さなどは、画像処理やAIでは判断が難しい場合があります。具体的には以下の例が存在します。
1)色味の違い
製品表面の色味の違いは定量化が難しく、自動化が難しい項目です。特に切削油を除去するための洗浄工程後におけるキズと水滴の識別や、銅基板の酸化による黒ずみとサビの識別などが代表例として挙げられます。こういった人間では官能的に判断している色味情報も、カメラのセンサー情報から画像ののRGB値で表現すると、非常に微細な絶対量の差であったり分布としての違いしかない場合が多く、コンピュータで識別するには至難な業となります。そのほか、色味の判断のルールを定量化することが難しく、人で感覚的に判断するケースがあります。例えば「黒色のサビは不良とする」という基準があったとして、白と黒の中間の色調の対象を見た時に、人によってどこからどこまでが「黒色」なのか判断が分かれてしまうというケースがこれに当たります。
通常の画像処理では基準の定量化が難しい場合も多く、結果として人による目視検査に頼ってしまうというケースが多いです。AIによって人の感覚のOK、NGの振り分けを学習させて検査させるような手法も出てきていますが、画像でも人が欠陥を判断可能であることは重要な前提事項となります。
(2)深さやパターン
製品表面に入るキズも、場合によっては定量化が難しくなります。たとえば、部品を切削して製造する場合の切削痕(ツールマーク)は良品と判定し、切削痕と異なる場合は不良としたいであったり、キズの深さという検査基準に対し、指で触った時に引っ掛かりがあるものは不良としたいが、引っ掛かりがないものは良品としたい、などが挙げられます。画像検査においては、前者は細かなキズ1つ1つを認識し、後者は画像にすると見え方が変わらないということから、良品と不良品の違いを読み取ることが非常に難しいことがあります。画像からは読み取り辛い情報を使った検査基準に対しては、画像検査によって自動的に切り分けるのは難しく、欠陥の程度が、輝度などの見え方の違いに出るような撮像の仕方などに落とし込むか、3D計測などの代替手段を考える必要があります。
(3)見え方の変化
特に打痕やへこみなど凹凸情報を含むような不良は定量化が難しい場合が多いです。人間の目視検査では手に取って角度を変えながら、怪しい箇所を回しながら確認することができるため検出できますが、画像検査においては、搬送状態や照明環境の当たり方が固定化された状態で画像になるため、状態によってはそもそも画像上に存在しないといった場合があるからです。対策としては、人間の動きを再現して、ロボットアームを用いた複数の角度から撮影することや、複数方向からの照明を当てて複数回撮像したりすることが考えられますが、コストや技術的な難易度が高くなることに留意する必要があります。
まとめ
これまで紹介してきた定量化の難しい項目も、画像処理技術の向上により徐々に対応可能となってきています。
特に良品・不良品の画像からAI自らが判定基準を学習する「ディープラーニング」という技術の発展により、従来は検査基準の定量化が難しかった領域においても、自動化が可能となりつつあります。
とはいっても、画像から様々な情報を読み解く画像検査においては、そもそも画像にしたときに情報が欠落していたり、コンピュータからは判断がつきづらい人間が目視で検査するために作り上げた検査基準に則った100%精度の外観検査というのは非常に実現するのが困難なのが実情です。
外観検査を自動化するには製造プロセスにおける前後工程の方々とコミュニケーションをとり、可能であれば目視検査用に作成された検査基準を画像検査用に変更するように、運用の基準を柔軟に適合していく必要も出てきます。
一方で、昨今の品質要求の高まりやSNS等の流行により品質トラブルが生じるリスクが高まっているのも事実ですので、そう簡単に現行の検査基準を変更することはできないこともあるでしょう。そういった場合は、画像検査で行える部分はしっかりと自動化し、画像検査では難しい部分を人間の手でおこなうという協業というやり方が考えられます。全てを自動化できないといけない、全てを切り分けないといけないのではなく、人と画像検査でできること適切に切り分け、現行の目視検査における工数や検査精度を改善していくことが肝要です。