外観検査で厳禁の不良の見逃し。見逃しパターンとその対策。
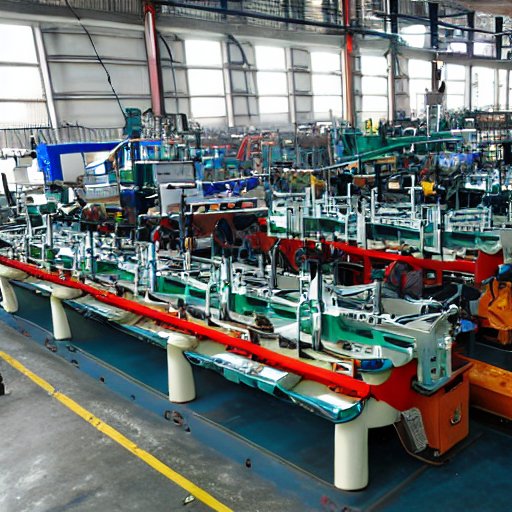
不良の見逃し
外観検査では、製品や部品の外観の特徴を評価し、外観や製品機能を損ない得る欠陥がないように品質の管理を行います。外観検査の役割には、以下の2点が挙げられ、規格に適合しない欠陥品を流出させてしまうと、膨大な回収コストが発生するうえに自社の信頼を大きく損ねてしまいます。このことから、自社のブランド価値を維持・向上していくには不良品の流出は何としても避けなければいけません。
- 欠陥品の市場流出を防止
- 製品品質の改善
事前に検査をすることで、欠陥品が発生した場合でも流出を防ぐことができ、検査により常時発生している不具合があると分かった場合は、その根本原因を確認・対応することで全体の品質改善が可能にもなります。外観検査を行うことで、「余計なコストの削減」「信頼の維持」「前工程の設備改善」といった効果があります。
なぜ見逃しが起こるのか
自社のブランド価値を維持・向上していくには不可欠な外観検査ですが、これまで多くの企業において市場流出が生じ、場合によってはリコールとなる事象がたびたび起きてきました。検査の重要性は誰しもが認識しているわけですが、なぜ見逃しが起きてしまうのでしょうか。目視検査を例に見逃しの発生要因を見ていきましょう。
- 人間の主観的な判断: 外観検査は、検査者が製品の外観を目視で評価する作業です。しかし、人間の目は主観的な要素や個人の感覚に左右される場合があります。検査者によっては、同じ製品でも判断基準や注意点が異なる場合があり、それによって不良品を見逃してしまうことがあります。
- 高速な検査ライン: 製造業では高速な検査ラインを採用していますが、この速さによって検査時間が制約される場合があります。検査者が短い時間内に多くの製品を確認する必要がありますので、見逃しやミスのリスクが増えます。
- 検査対象の特殊性: 製品の外観には多様な特徴があります。微細な傷、不均一な色、微妙な形状の違いなど、見逃しや判断の難しい欠陥が存在する場合があります。特に、微細な欠陥や、微妙な不均一さを検出することは困難であり、見逃しのリスクが高まります。
- 疲労や集中力の低下: 長時間にわたる外観検査作業は、検査者の疲労や集中力の低下につながる可能性があります。疲労が蓄積すると、見逃しやミスの確率が上がります。また、単調な作業や反復作業による集中力の低下も見逃しの原因となります。
- 検査方法や機器の制約: 外観検査に使用される方法や機器にも制約があります。一部の欠陥や不良箇所は、使用される検査方法や機器では検出が困難な場合があります。検査方法や機器の改善が必要となる場合もあります。
その他、昨今の人材不足による既存の検査員への負担増大などが挙げられますが、見逃しが起きてしまう原因は単純なものではなく、様々な要因が複合的に入り混じったものです。
対策として、経験やコツに頼らない検査基準の明確化や経験の浅い社員への教育などが考えられます。誰がいつ行っても同じ検査が行えるというのが優れた検査と言えるのではないでしょうか。
いつ行っても同じ検査が行うためには、目視ではなく、画像検査を用いた自動検査によって検査を画一化し高速かつ高精度に行うということが考えられます。目視検査をどの検査員が行っても同じ品質で検査が行える状態を作り上げるよりも、画像検査を導入した方が高精度かつ長い目で見た時に投入コストが小さく済むということも考えられます。ただ、検査を自動化することのメリットは大きいですが、それでも不良品を見逃してしまうリスクは少なからず存在します。
画像検査における見逃しパターン
画像検査に用いられる手法として、画像処理やAIがあります。それぞれのケースで見逃しが発生する場合の例を以下に挙げます。
画像処理の場合
- 新しい不良パターンへの対応:例えば不良の色で検査のアルゴリズムを作成していた場合に、想定した色と異なる不良が出ることで見逃しをしてしまう。
- 良品と似た不良パターン:通常のと汚れと傷が、画像上で見分けがつきにくいケースがあり、過検出を防ぐ閾値で未検出が発生してしまう。
- マスク領域:過検出が多いため、マスク処理により検出をしないようにしていた領域で、不良が発生する。
AIの場合
- データの偏り: AIの学習に使用するデータセットは、様々な種類の正常品と不良品を含む必要があります。しかし、データセットが不十分であったり、特定の不良パターンが不適切にサンプリングされている場合、モデルは不良品を適切に検出できない可能性があります。画像処理においても特定の不良や品種においてアルゴリズムを作成したものでは、異なる不良や品種において見逃すリスクが高まります。
- 新しい不良パターンへの対応: AIモデルは訓練データに基づいて学習します。しかし、新しい不良パターンが現れた場合、モデルはそれを適切に検出する能力に欠ける可能性があります。モデルは学習した製品と似た見た目の対象しか検出ができないため、新たな不良パターンに対して再トレーニングやアップデートが必要になる場合があります。画像処理においても、予期しない不良パターンに遭遇すると、アルゴリズムに抜け漏れが生じることとなり、結果として見逃しが起きてしまいます。
- 検査対象の制約: 画像処理やAIを使用した検査では、製品の画像データが必要であり、実際の運用において学習した画像と同様の見え方をしている必要があります。しかし、搬送のバラつきによって様々な位置で製品が撮影される場合において、角度や視点で網羅的に撮影できていないと、見え方や照明の映り方により色味に乖離が生じる恐れがあります。そのため、事前の学習や画像処理のルール構築段階において、このような映り方の違いを考慮しておかないと、不良品が適切に検出できない場合があります。また、製品の形状や材料によっては、画像の品質や解像度の制約が生じる場合もあります。
- 良品と似た不良パターン:学習した画像に良品と似た見た目をした対象が含まれている場合の見逃しや、不良と判定するための設定したしきい値近辺の対象においては照明の当たり方などによって良品として判定してしまう例などが挙げられます。
このように、画像検査においても見逃しが生じるリスクは存在しているのです。画像検査において重要になってくるのが、いかに網羅的な不良パターンを想定し、学習画像や画像処理ルールの構築に反映させるかということが考えられます。とは言っても、網羅的に発生しうる不良パターンを把握することは難しいので、想定外の不良パターンに対応し市場への不良品の流出を防止できるように想定・対策しておく必要があります。
人間と自動検査の組み合わせ
人間の目視検査においては、作業者によって判定が変わることや、作業の疲労によって集中力が低下するなど、いつでも同じ品質で検査を行えないといった点で見逃しのリスクがあります。一方のAIや画像処理を用いた自動検査においては、学習画像やルールの構築が網羅的でないと不良品を見逃すリスクは存在しているというのは、先述した通りです。
目視検査や画像検査を用いた自動検査の品質を追求し、品質を高めることで見逃しを限りなく0に近づけることはそれぞれ1つの手法として考えられます。ただ、多くの場合精度を追求することによって時間や金額のコストがかさんでしまいしまいます。
そこで目視検査と画像検査を並行して行い、それぞれが得意な範囲を担当し最小限のコストをもって見逃しを減らしていくというアプローチが考えられます。画像検査が得意な事前に学習やルールに反映した不良は確実に検出ができるという強みと、目視検査が得意な柔軟に対応がとれるという強みを組み合わせることで、目視検査や画像検査単体の精度追及よりも少ない投入コストで見逃し0の検査が実現しうる訳です。画像検査で万一不良品を検出できなかった場合でも、目視検査の2回目のチェックによって市場への流出を防ぐことができます。